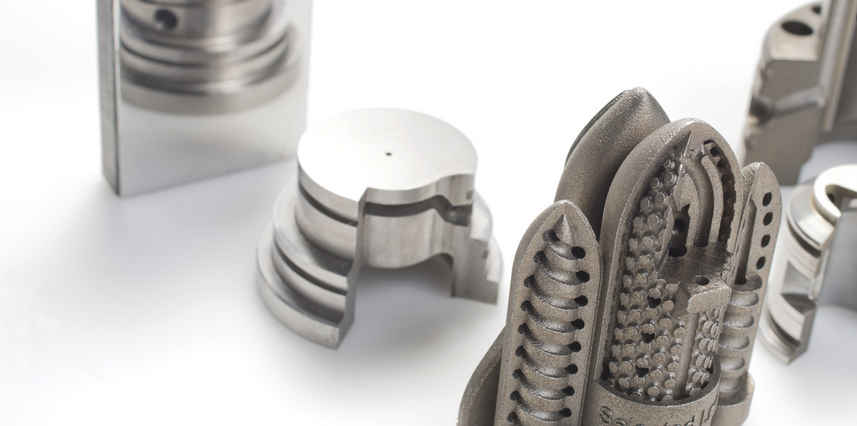

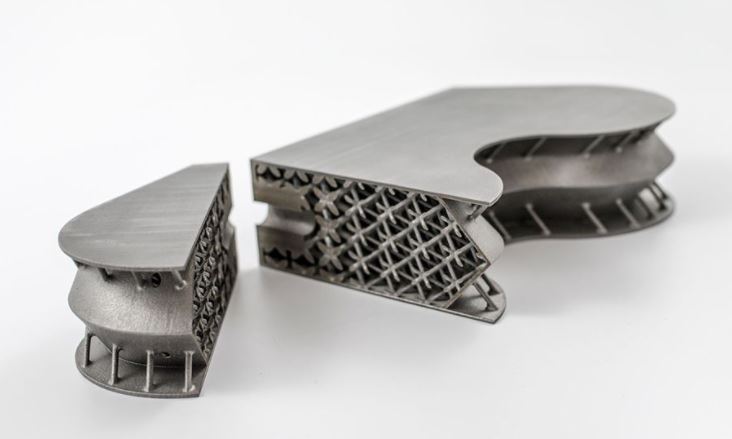
Selective Laser Melting (SLM) Additive Manufacturing Process
SLM is one of the most exciting 3D printing technologies available today and is utilized both for rapid prototyping and mass production. The range of metal alloys available is fairly extensive. The end result has properties equivalent to those manufactured via traditional manufacturing processes. SLM creates parts additively by fusing metal powder particles together in a full melting process. SLM fully melts the powder, and therefore it needs to reach a higher temperature than this other metal 3D printing technique. The build chamber is filled with an inert gas (either argon or nitrogen at oxygen levels below 500 parts per million) in order to create the perfect conditions for melting. The full melting process allows the metal to form a homogeneous block with good resistance. It fits perfectly for pure metals like titanium or aluminum. Because we need the higher temperature to fully melt the material, the cooling time will be longer than for DMLS. SelectiveLaser Melting process uses supports in order to reinforce small angles and hangovers of the parts but also to stick the design to the job tray.The support will be removed manually after cooling. Various finishing techniques such as milling, thermal treatment or touring are commonly used after the print in order to achieve the functionnal requirements ofthe part. Aluminum Alloys-AlSi10Mg AlSi10Mg is a hardenable aluminum-alloy widely used in additive manufacturing suitable for thin-walled components with high corrosion resistance, as well as thermal and electrical conductivity properties. Featuring a nearly non-porous texture, it is ideal for highly stressed parts maintaining dynamic load capacity.
The Advantages of SLM 3D
• fast production possible
• complex shapes with complex internal structure possible
• no design limitations • use of very high-quality materials
• reduced development cycle
• increased productivity
• reduced weight
• material and energy savings
• use of new alloys
• access to innovative ideas
Unlimited Process Contermad
has gained extensive experience with 3D metal printing. We can print using various materials, including stainless steel, titanium, aluminum and tooling steel. The metal characteristics after printing virtually equal the standard characteristics of the metal. Compared to conventional technology, 3D metal printing offers unlimited possibilities for companies in various branches. Contermad is known for its extensive know-how of materials. When it comes to printing metal products, we can advise on material that is best suited for your application.
– Maraging steel 1.2709
– H13 steel 1.2344
– Aluminum AlSi10Mg
– Stainless steel 1.4542
– Titanium Alloys
Mechanical Property of Metal Powder
Maraging Steel(1.2709 Tool Steel)
Tool steels such as 1.2709 are primarily used for manufacturing tools and molds. They are characterized by a high hardness combined with a high ductility. Their specific mechanical properties allow usage in high-stressed components due to its high wear resistance.
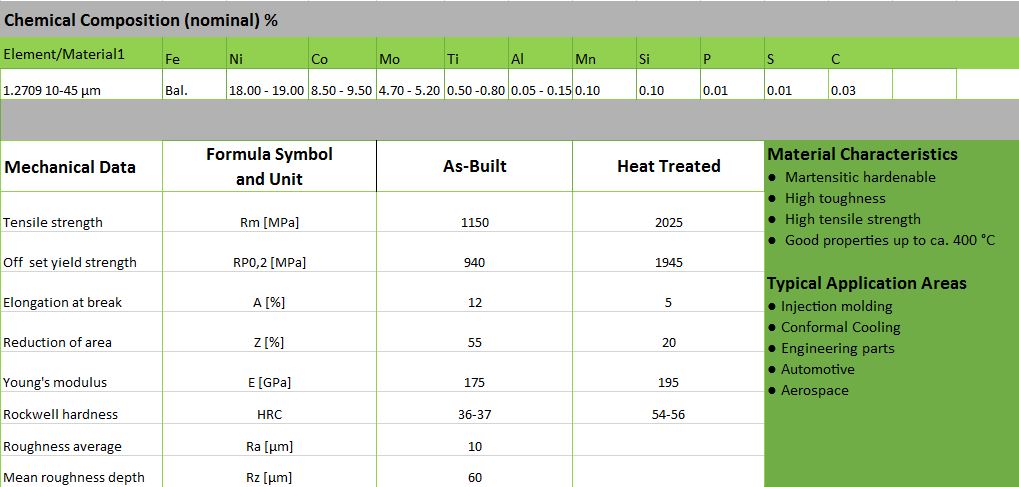
H13 Steel (1.2344)
H13 (1.2344) is a chromium containing martensitic tool steel. This material is resistant to thermal fatigue cracking and is used in tooling applications that require exceptional strength and toughness.
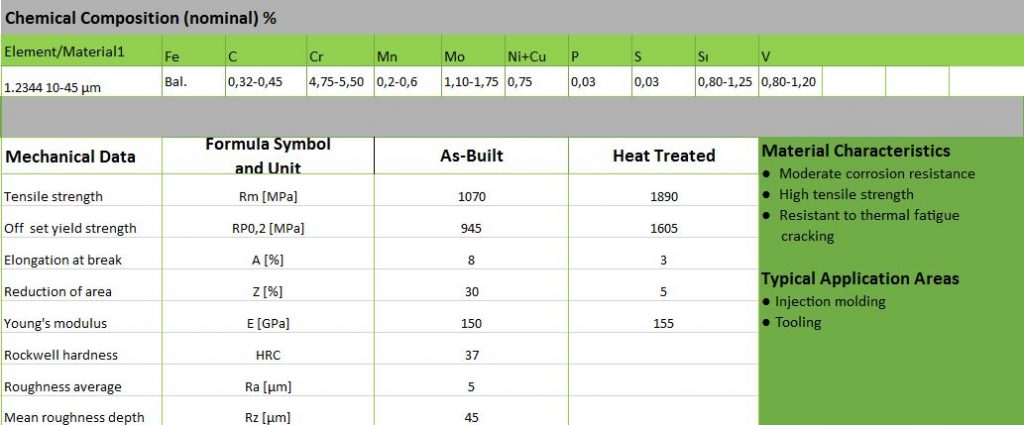
Aluminum Alloys-AlSi10Mg
AlSi10Mg is a hardenable aluminum-alloy widely used in additive manufacturing suitable for thin-walled components with high corrosion resistance, as well as thermal and electrical conductivity properties. Featuring a nearly non-porous texture, it is ideal for highly stressed parts maintaining dynamic load capacity.
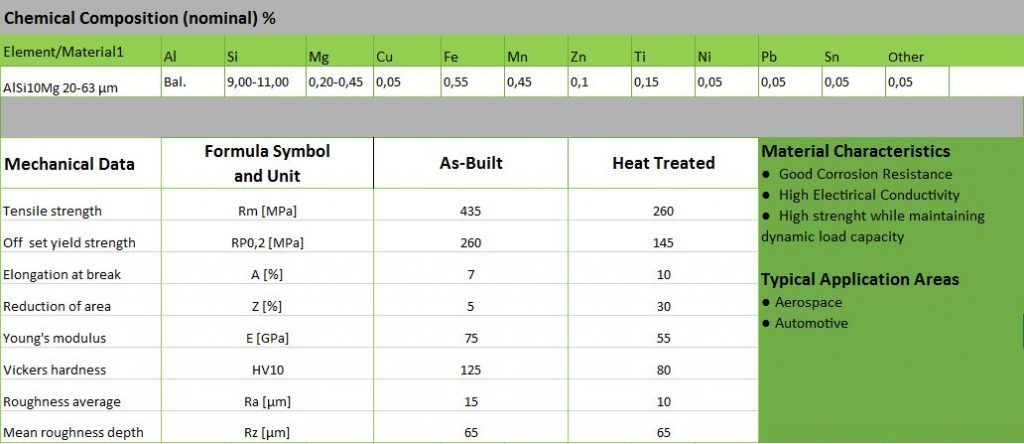
Stainless Steel (1.4542)
1.4542 is a martensitic precipitation-hardenable Cr-Ni-Cu-steel possessing high strength and toughness. A versatile material, it provides an outstanding combination of good corrosion resistance and mechanical properties at temperatures up to 320 °C and is suitable for heavy-strain applications, thanks to its high wear resistance.
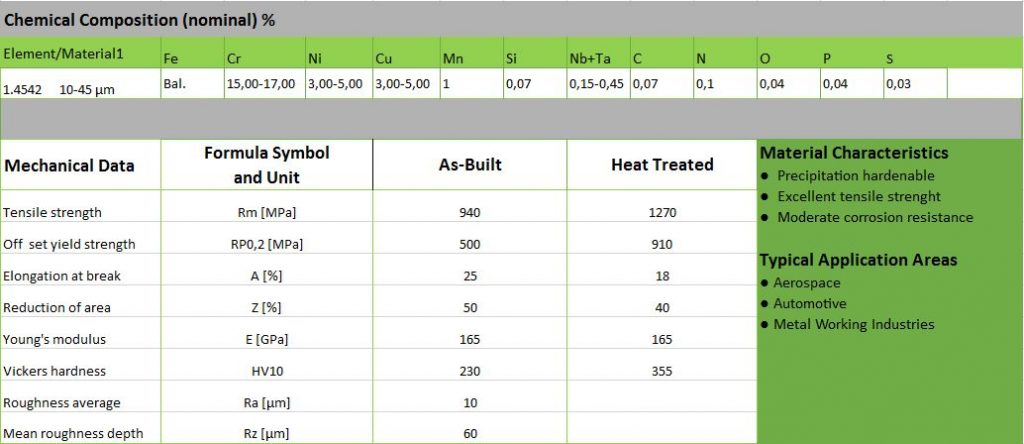
Ti6Al4V Titanium Alloy
Ti6Al4V is the the most widely used titanium-based alloy in the world. Ti6Al4V stands out because of its thermal expansion coefficient, biocompatibility, high strength at low density and excellent corrosion resistance.
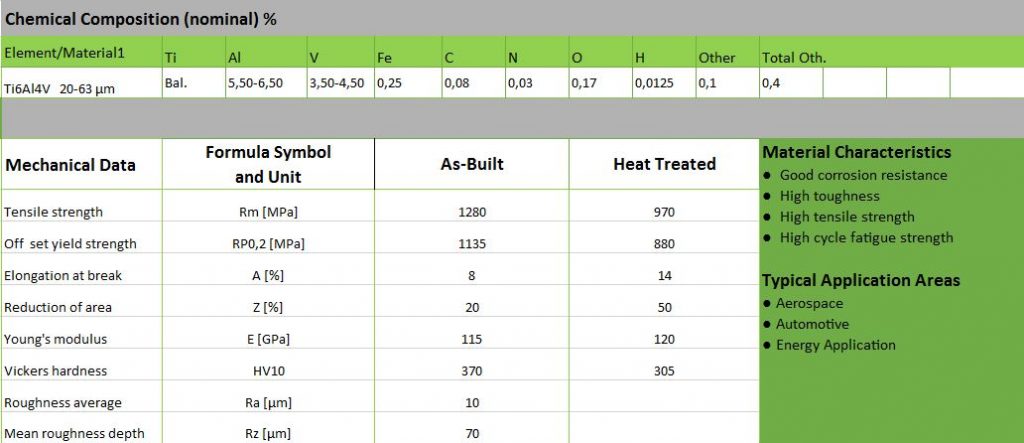